Der gezielte Einsatz von Wärme und Kälte verändert bei einer enormen Bandbreite von Metallen sowie Metallwerkstoffen deren physikalische und technische Eigenschaften – teils dauerhaft, teils nur, solange die Temperatur aufrechterhalten wird. Dadurch ergeben sich ebenfalls sehr breite Optionen, um Metallprodukte mit exakt vorhersehbaren Eigenschaften anzufertigen. Sechs besonders wichtige Verfahren stellen wir jetzt vor.
Denn je nach Grundmetall und exakter Legierung wird durch derartige Temperatureinwirkungen eine – stark vereinfacht formuliert – Veränderung im Gefüge hervorgerufen. Diese Effekte können sowohl genutzt werden, um Metallwerkstoffe einfacher oder gar überhaupt in eine gewünschte Form zu bringen, als auch, um nach der Ausformung die späteren mechanischen und anderen Werkstoffeigenschaften zwischen Härte, Zerspanbarkeit und Zugfestigkeit präzise einzustellen – natürlich nur im Rahmen der Grenzen der Ausgangslegierung. Die wichtigsten Verfahren und ihre Effekte, respektive Auswirkungen stellen wir auf den folgenden Zeilen vor.
Inhaltsverzeichnis
1. Gießen
Metalle können durch ausreichendes Erhitzen eine stark fließfähige Konsistenz erreichen. Wird keine weitere Wärme mehr zugegeben, erfolgt eine allmähliche Erstarrung. Gießen macht sich diese Eigenschaften zunutze – und es wird aus drei guten Gründen an erster Stelle dieser Liste genannt:
- Von allen gängigen Verfahren werden hierbei die mit Abstand höchsten Temperaturen angewendet. Genauer: Solche, die genügen, um die Ausgangsmetalle und alle anderen Legierungselemente in einen flüssigen Zustand zu bringen. Der Viskositätsgrad (und somit die Gieß- und Fließfähigkeit) unterscheidet sich dabei unter anderem durch die exakte Legierung. Er reicht von nahezu wasserflüssig bis honigflüssig.
- Fast alle Metallwerkstoffe sind Legierungen, also metallische Gemische aus wenigstens zwei Grund-Elementen. Um sie herzustellen ist ebenfalls ein Verflüssigen aller Bestandteile nötig.
- Bei einer erheblichen Majorität aller Metallwerkstoffe wird die Schmelze sowieso in Formen gegossen, um durch diesen Urformschritt zumindest leichter handhabbare Halbzeuge mit bekannten Daten zu erhalten. Etwa exakte Volumina oder Abmessungen. Beispielsweise wird Rohmetall, das nicht sofort weiterverarbeitet wird, standardmäßig in Barren oder andere einfache geometrische Formen gegossen.
Rein technisch betrachtet kann das Gießen deshalb sowohl ein Zwischenschritt zu Beginn eines längeren Verarbeitungsprozesses sein als auch ein abschließender – zumindest, was die Wärmebehandlung anbelangt. Beispielsweise kann es bei simplen Produkten aus Gusseisen bereits genügen, diverse Gussputz-Verfahren anzuwenden, um den Gegenstand oberflächlich zu säubern und so verkaufsfertig zu machen.
Was das Gießen selbst anbelangt, so stehen je nach Metallwerkstoff und gewünschtem Endprodukt mehrere unterschiedliche Verfahren zur Auswahl – maßgeblich ist dabei vor allem die Art der Gussform und des Einbringens der Schmelze. Ihnen allen gemein ist jedoch unter anderem eine große Ökonomie:
Basierend auf Kenntnissen, wie etwa dem Schrumpfungsverhalten bei Abkühlung, lassen sich die nötigen Schmelze-Mengen exakt vorhersagen. Dadurch sind Materialverluste von teils deutlich unter einem Prozent machbar. Gleichsam können kostspielige spanabhebende Weiterverarbeitungsschritte mitunter gänzlich vermieden werden.
Nicht zuletzt gestatten es verschiedene Gießverfahren, geometrisch sehr komplexe Formen anzufertigen, die sich anderweitig nur durch langwierige und technisch sehr aufwendige spanabhebende Nachbearbeitung erzielen ließen – wenn überhaupt. So werden beispielsweise Motorblöcke nahezu ausschließlich gegossen, obwohl (und weil) sie von einer Vielzahl von Kühlflüssigkeits- und Ölkanälen durchzogen sein müssen.
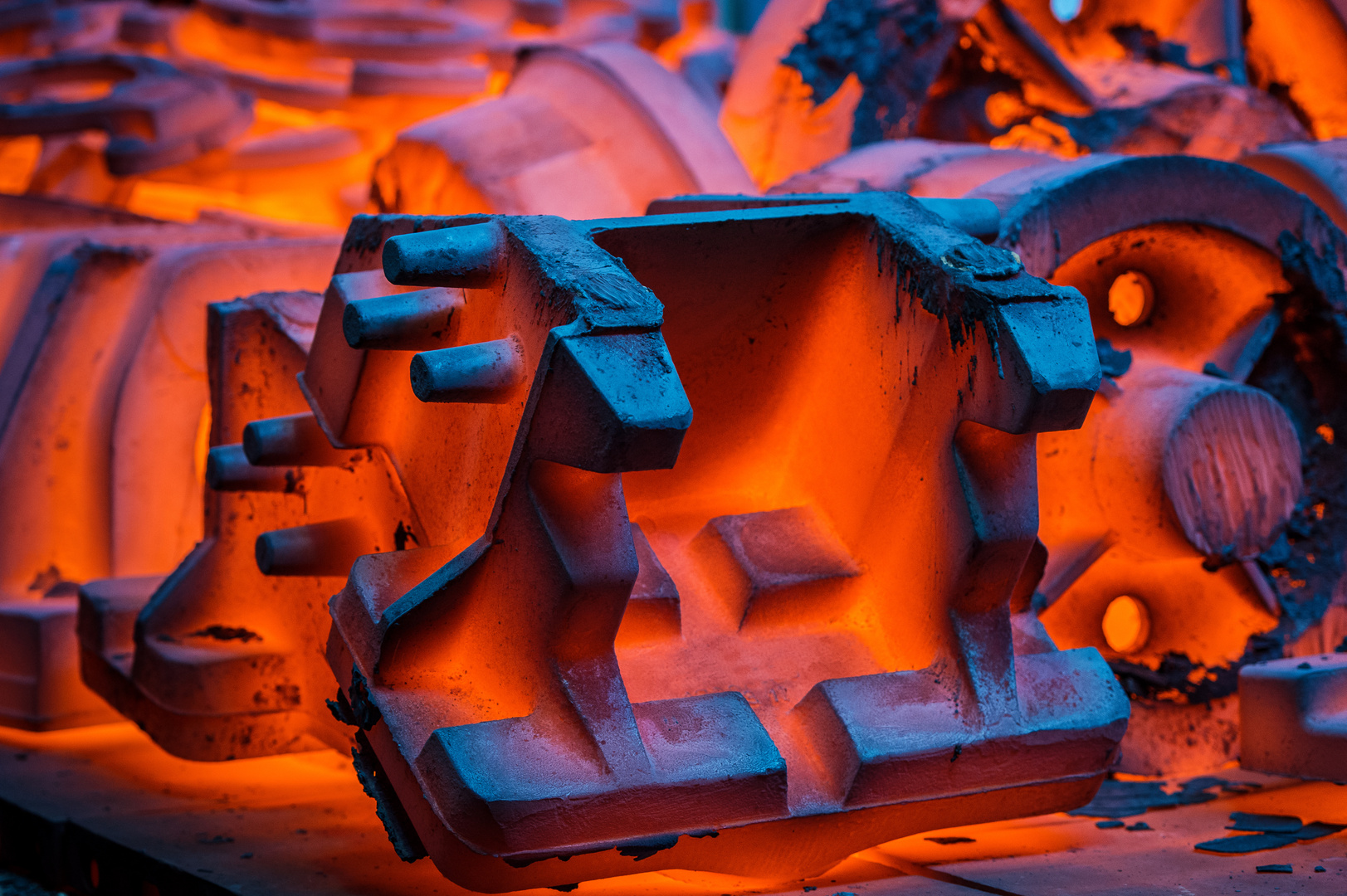
2. Warmschmieden
Bei vielen Metallprodukten folgt das Schmieden als zweiter Bearbeitungsschritt, nachdem das Gießen für das Urformen zuständig war. Der zentrale Wesenskern des Schmiedens, es wird gezielt Druck auf das Halbzeug ausgeübt. Dadurch entstehen zwei maßgebliche Effekte:
- Formveränderung:
Aufgrund des Impakts eines Hammers oder eines ähnlichen „Druckgebers“ wird Material verdrängt. Bei der einfachsten Technik, dem manuellen Freihandschmieden, stellen nur Hammer und Amboss die räumlichen Grenzen dar. Bei industrielleren Verfahren, etwa dem Gesenkschmieden, wird der Metallwerkstoff hingegen unter enormem Druck in eine Negativform hineingepresst, die dadurch eine exakte räumliche Grenze vorgibt. - Gitterverdichtung:
Aufgrund des Drucks wird das Gefüge im Metallwerkstoff verändert – konkret: verdichtet. Dies wirkt sich teils dramatisch auf die Festigkeit auf, die hierdurch gesteigert wird.
Technisch gesehen unterscheiden sich verschiedene Schmiedeverfahren hauptsächlich über die Temperatur des Werkstücks. Das wichtigste ist das Warmschmieden. Die Arbeitstemperatur hierbei liegt stets oberhalb der Rekristallisations- respektive Solidustemperatur des Werkstoffs. Einfach ausgedrückt: Das Metall ist nicht mehr vollständig fest, jedoch nicht im Zustand einer flüssigen Schmelze. Das Ergebnis ist ein sehr zäher, Teig-artiger Zustand.
Die Vorteile für die Verarbeitung:
- Deutlich verringerter Kraftaufwand für die Umformung.
- Generell größere plastische Verformbarkeit ohne Materialbruch.
Die Schwierigkeit entsteht durch die Temperaturbereiche vieler Metalle. Zwar werden die meisten heutigen Metallwerkstoffe geschmiedet bzw. können geschmiedet werden. Dies ist jedoch nur möglich, weil komplexe Verfahren ersonnen wurden, um das mitunter sehr enge Fenster zwischen Solidus- und vollständiger Verflüssigungstemperatur zu beherrschen.
Ob ein Metallwerkstoff überhaupt schmiedefähig ist, hängt zudem stark von seinen Legierungsbestandteilen ab. Bei Gusseisen, als prominentestem Vertreter, ist der Kohlenstoffgehalt zu hoch. Hier existiert kein Temperaturfenster, in dem das Material Teig-artig und verformbar wäre. Selbst im glühenden, aber noch weitgehend festen Zustand würde das Gusseisen unter dem Druck zerspringen. Es kann nur durch vollständige Verflüssigung und erneutes Gießen umgeformt werden.
Übrigens: Zwar ist das Walzen technisch betrachtet ein anderes Verfahren als das Schmieden. Da hier jedoch ebenfalls mit großem Druck gearbeitet wird, sind Herangehensweise und Zielsetzung zumindest vergleichbar.
3. Härten durch Abschrecken
Auf einer kristallinen Ebene können sehr viele Metallwerkstoffe durch den Grad von Erhitzung und Abkühlung sowie den dafür nötigen Zeitfaktor sehr umfassend justiert werden. Eine der wichtigsten Techniken, die dieses Prinzip ausnutzt, ist das Härten unter Einsatz von Hitze. Da sich die Vorgehensweisen und das Verhalten stark vom jeweiligen Metallwerkstoff unterscheiden, sei an dieser Stelle nur das grundsätzliche Prinzip erläutert: Hierbei wird das Material über eine Temperatur gebracht, bei der sich die Atomgitter verändern.
Durch das gezielte Abschrecken in einem deutlich kälteren Medium wird dieser Zustand erhalten. Bei einem langsameren Abkühlen würden die Atomgitter hingegen wieder ihren Ausgangszustand einnehmen. Der wichtigste Grund für das Härten besteht bei Eisen-, respektive Stahlwerkstoffen darin, die mechanische Widerstandsfähigkeit der jeweiligen Legierung zu maximieren.
Je nach Herangehensweise kann dabei das gesamte Werkstück oder nur ein Teil davon gehärtet werden – beispielsweise nur der Schneidbereich einer Klinge oder die obersten Millimeter einer Stahlplatte. Dies gestattet es, einem Werkstück hart-zähe Eigenschaften zu verleihen.
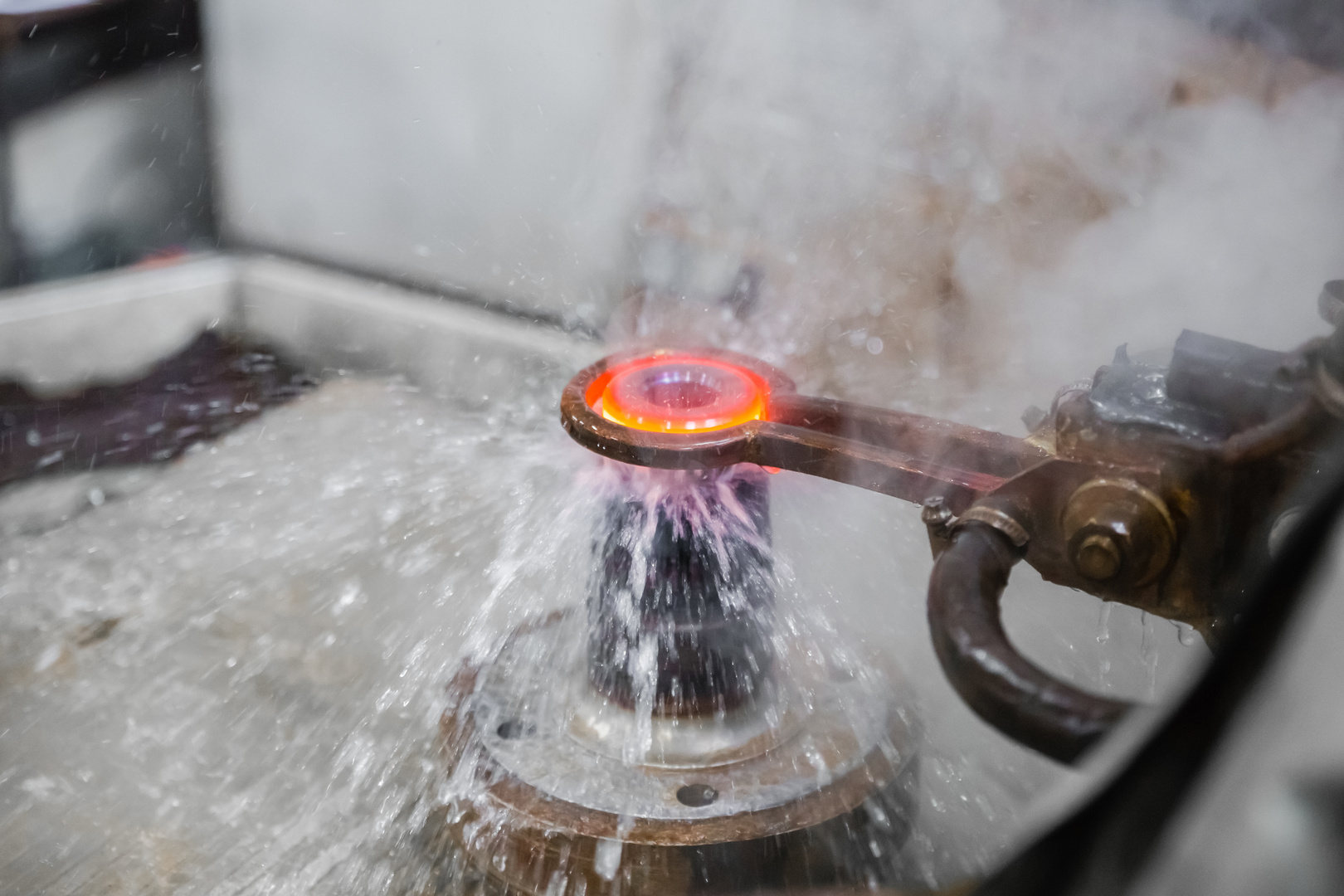
4. Weichglühen und Anlassen
Das Härten kann ein mitunter zu hartes Produkt hervorrufen. Je nach weiterem Verwendungszweck wird deshalb häufig in einem Folgeschritt abermals Wärme appliziert. Dabei bestimmt die Zielsetzung, wie hoch die Temperatur geht.
- Soll ein Metall lediglich wieder seinen bei Raumtemperatur geringsten Härtegrad erreichen, wird dabei eine ähnliche Temperatur erzielt wie beim Härten – bloß ohne anschließendes schockartiges Abschrecken.
- Beim Anlassen hingegen werden niedrigere Temperaturen genutzt. Dadurch werden im Gefüge lediglich Spannungen abgebaut. Das reduziert die maximale Härte, sorgt jedoch für einen zäheren Werkstoff.
Zusätzlich kann geglüht werden, um einen Werkstoff, der durch kaltes Schmieden zu hart geworden ist, wieder in einen nutzbaren Zustand zu bringen. Prominent ist das bei Kupfer der Fall.
5. Brennschneiden
Bei vielen Halbzeugen und (Vor-) Produkten aus Metallen ist es nötig, Material abzutragen. Das, um entweder eine endgültige Formgebung zu erreichen oder einen Gegenstand am Ende seiner Nutzung auf für das Recycling besser handhabbare Abmessungen zu bringen. An dieser Stelle sei auf den enormen Recyclinggrad von Metallen verwiesen, der je nach Material gen 100 Prozent tendiert.
Für diese Materialabtragung stehen unterschiedlichste mechanische Verfahren zur Verfügung. Viele davon unter Einsatz sehr harter Werkzeuge – etwa aus Korund. Welches genutzt wird, ist vielfach eine reine Frage von ökonomischen Faktoren wie benötigte Zeit und Kosten der Schneidwerkzeuge.
Bei vielen Metallprodukten ist das Brennschneiden die oftmals ökonomischste Lösung. Mithilfe
- eines Brenngas-Sauerstoffgemischs,
- eines elektrisch erzeugten Lichtbogens oder
- eines Lasers
wird dabei das Material räumlich sehr scharf umrissen erhitzt. Und zwar bis deutlich über die Verflüssigungstemperatur. Hierdurch entsteht am Werkstück eine Fuge, innerhalb der das Metall durch Verflüssigen abgetragen wird – also ein thermischer Schnitt. Sowohl der Rest des abzutragenden Materials als auch des Werkstücks bleiben unbeeinflusst.
Mitunter ist es jedoch aufgrund der hohen thermischen Belastung nahe der Schnittkanten anschließend nötig, das Werkstück (erneut) zu härten und gegebenenfalls anzulassen, um die ursprüngliche Charakteristik wiederherzustellen.
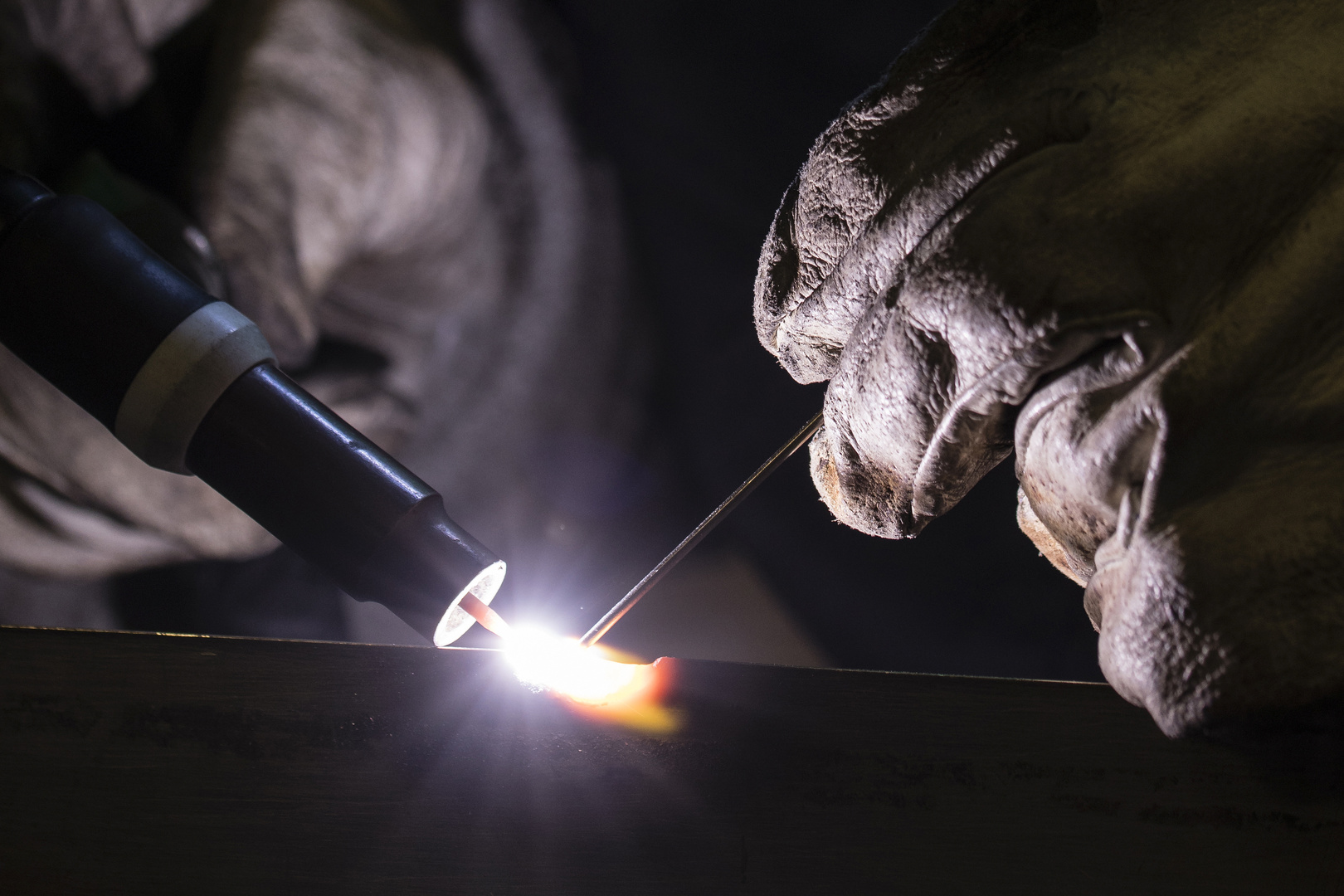
6. Schweißen
Das Schweißen verhält sich zum Brennschneiden ähnlich wie das Weichglühen zum Härten – also zwei eng miteinander verwandte Herangehensweisen. Beim Schweißen lautet die Zielsetzung allerdings, zwei bislang getrennte Werkstücke auf einer atomaren Ebene miteinander zu verbinden. Je nach Schweißverfahren und Güte der Durchführung sind selbst unter dem Mikroskop keine Unterschiede mehr zu erkennen.
Ganz grob lassen sich die folgenden Herangehensweisen unterscheiden:
- Schweißen ohne Hilfsfügematerial:
Hierbei genügt es, die Werkstückkanten aufzuschmelzen, bis die Schmelzen sich durch Ineinanderfließen miteinander verbinden. - Schweißen mit Hilfsfügematerial:
Hierbei werden nicht nur die Werkstückkanten aufgeschmolzen, sondern es wird beim Schweißen ein zusätzliches Material eingebracht – typischerweise ein zum Material passender Draht. Das ist beispielsweise nötig, wo große Lücken zu füllen sind.
Ebenfalls ähnlich wie beim Brennschneiden sind die typischen Hitzequellen. Also ein Gas-Sauerstoff-Gemisch, elektrischer Strom bzw. dessen Widerstand sowie Laser.
Da insbesondere Eisenmetalle durch die starke Erhitzung an der Stelle oxidieren, ist es vielfach nötig, die Schmelze gegen den Luftsauerstoff abzuschirmen. Dies geschieht beispielsweise durch inerte oder mit dem Metall reagierende Gase wie Argon oder Kohlenstoffdioxid oder durch eine aufschmelzende, Schlacke-bildende Ummantelung oder Füllung des Hilfsfügematerials.